EchTherm Updates
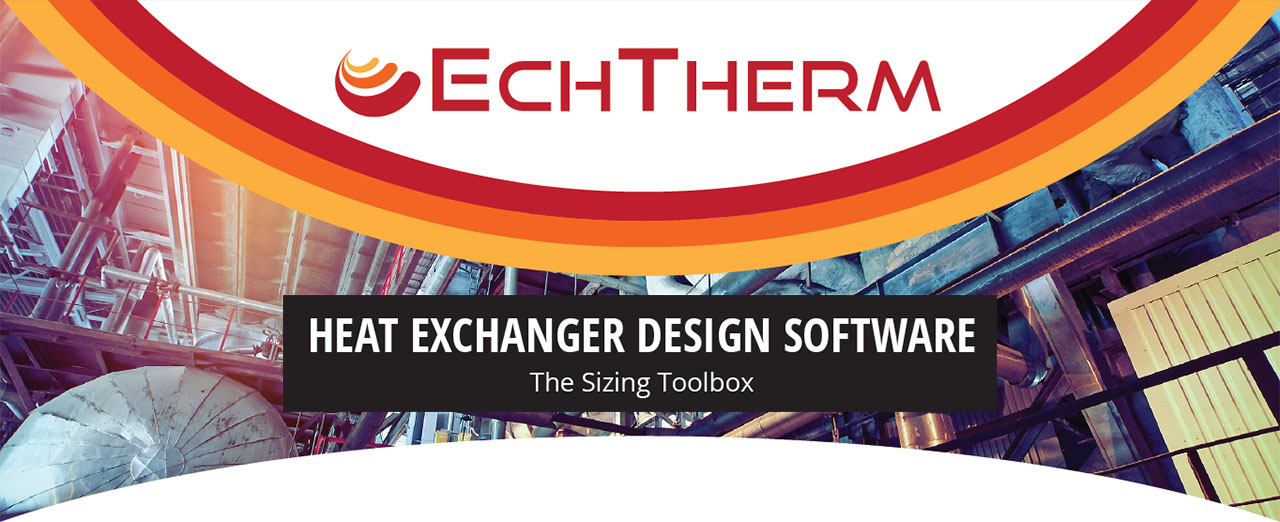
Download EchTherm | EchTherm Flyer | Instruction manual |
For each version below, there are various debugging / corrections / improvements to the calculation code, and corrections / improvements to the interfacing. Only the main additions/modifications are presented below for each section of the software.
Updates / New features 8.0.3 (Date: 01st August 2025)
Debugging & Improvements:
- Adding of fluid Midel 7131 in single-phase computer programs.
- Improvement of humid air model in single-phase computer program for Smooth Tube Bundle Heat Exchanger and Circular Finned Tube Bundle Heat Exchanger (Sizing computer program only) to take into account the possibility to calculate thermophysical properties of humid air above 100°C.
- Debugging of single-phase Plate Heat Exchanger computer program (Sizing and Simulation): Correction of the correlation for the evaluation of friction factor and Nusselt number on the hot side.
- Debugging various computer programs in two-phase flow mode (Sizing and Simulation) to take into account the possibility to calculate heat exchanger performance for Argon, Nitrogen and Oxygen in two-phase flow (older versions cannot calculate the thermal conductivity at vapor saturation state).
- Modification of Shell and Tube Heat Exchanger computer program for NTIW baffle type (No Tube in Window).
- Various debugging and improvement (especially on interface/display and plots).
Updates / New features 8.0.2 (Date: 23th May 2025)
Debugging & Improvements:
- Correction of corrective factor (called “CTherm“) for single-phase shell side correlation when operating conditions are supercritical in computer programs dedicated to Shell & Tubes technology.
- Improvement of time calculation, optimisation and correction of heat transfer and friction factor correlations in various plate heat exchanger computer program (simulation, sizing & expertise)
- Improvement of the calculation precision for cost estimation for shell and tube heat exchanger in dedicated TOOLS+ computer program
- Various debugging and improvement (especially on interface/display and plots)
Updates / New features 8.0.1 (Date: 06th February 2025)
Debugging & Improvements:
- For Shell & Tube Heat Exchanger computer program, only in SIZING mode and only for TEMA shell type E : Bug fixing to eliminating an untimely error message (this made it impossible to make a backup)
- Add nozzle velocity information in the interface for single-phase plate heat exchanger computer program (already available in diphasic plate heat exchanger)
Updates / New features 8.0.0 (Date: 24th January 2025)
General:
- NEW DESIGN (more user friendly) for a better user experience,
- The main interface of the software has been rearranged:
o In Sizing Category, for Shell and Tube technology, the layout is now organized by the different TEMA groups;
o In the Tools+ section, there is a global rearrangement to place the most closely related sheets on the same row.
New computer program:
- Sizing computer program for TEMA F Shell & Tube Heat Exchanger in Single-Phase.
- Simulation computer program for Smooth Tube Bundle Heat Exchanger in Single Phase.
- Tools+ computer program “Shell & Tube Heat Exchanger Diagram Generator”: This tool can create a diagram of the S&T heat exchanger according to your geometrical input. You can visualize the true number of tubes in the bundle, the arrangement/configuration, the number of baffle and the different clearance. This tool is automatic linked to S&T sizing & simulation software.
Other improvement:
- “Unit Conversion” computer program in Tools+ category has been improved. It can be used quickly and easily to convert all the units used in thermal field. Find all the different unit on the dedicated calculated program.
- Different adding and improvements of correlation for different technologies (plate heat exchanger, finned tubes bundles, etc.)
- Improvement of the taking into account of humid air condensation (especially for partial surface condensation) for concerning technologies;
Updates / New features 7.2.6 (Date: 21st March 2024)
Sizing & Simulation:
- Modification of warning message for shell and tube heat exchanger technology regarding the size comparison between the tube bundle diameter and the shell diameter.
- Improvement of convergence criteria and time convergence for Coil Wound heat exchanger technology in simulation mode.
- Extension and Precision Addendum on Correlation Validity Area for Continuous Finned Tube Heat Exchangers technology.
- Correction of diphasic pressure drop correlation for plate heat exchanger technology in evaporation and condensation.
Expertise:
- Correction and modification of the Steiner & Taborek (1992) correlation in the evaporation in plain tube computer program.
General:
- Various minor display modifications and export debugging.
Updates / New features 7.2.5 (Date: 26th January 2024)
Sizing & Simulation:
- The choice of personal thermophysical properties is now available with interpolation and extrapolation between two point distinct from the process condition for all technologies.
- Improvement of the meshing in some SIZING computer programs (single-phase Shell and Tube, Tube-in-Tube, Plate, Spiral Plate Heat exchangers) in order to better take into account, the variation of the thermophysical properties (especially for high temperature differences between the inlet and outlet) and to obtain more accurate results.
- Display of Fluid Mass value is now available for all technologies in « Thermohydraulic » interface.
- Display of Nozzle ρV² value is now available for some technologies, especially for Shell and Tube Heat Exchanger, in «Thermohydraulic» interface and also in specification datasheet.
- U-Tube rear End Head option is now available on Single-Phase Shell and Tube Heat Exchanger
- Improvement of geometrical input for Shell and Tube Heat Exchanger (take into account of tubular plate thickness, inlet and outlet baffle spacing can be now different, etc.).
- Number of Fed-tube or Fed-channel are displayed for technology with several passes, and a warning message appears when this number is a non-integer number (more complex circuit).
- Improved calculation for singular pressure drops on bend for two-phase fluid heat exchanger.
- Different new warning messages for Shell and Tube Heat Exchanger to guide the user.
- For Plate Heat Exchanger, it is now possible to run calculation with a dimensionless pitch (ratio of corrugation pitch on corrugation height) higher than 3,33 and less than 2.
- Different adding and improvement of correlation.
Expertise:
- Improvement of results display: named of the selected heat transfer and friction factor law are now showing on results and flow regime is now display.
General:
- Harmonization, update and improvement of the different documents: notice, information documents in each computer program with more precise assumptions and limits, help file, etc.
Updates / New features 7.2.4 (Date: 25th July 2023)
Sizing & Simulation:
- Integration of new calculation sheet in simulation mode dedicated to the technology called "Circular Finned Tube Bundle Heat Exchanger" in single-phase flow.
- Improvement of meshing in simulation tools of Coil Wound Heat Exchanger
Updates / New features 7.2.3 (Date: 28th April 2023)
Technology Decision Support:
- The title of the "Single-Phase / Single-Phase Heat Exchanger" form has been changed to "Liquid / Liquid Heat Exchanger" to be consistent with the other forms in this tab.
- In the "Liquid / Liquid HE", "Gas / Liquid HE" and "Gas / Gas HE" calculation sheet, information about the chosen criteria is displayed directly on the interface according to the number in the drop-down list (previously displayed only in the help PDFs).
Sizing & Simulation:
- Integration of the first phase change simulation sheet of the software: new sheet dedicated to the technology called "Continuous Finned Tube Bundle Heat Exchanger" with intratubular evaporation in simulation.
- Addition of the BEST DESIGN option on the "Continuous Finned Tube Bundle Heat Exchanger - Single-Phase Fluids" sheet.
- Improved calculations of external flow sections, as well as increasement factor for the "Circular Finned Tube Bundle Heat Exchanger" technology.
- Addition in the " THERMOHYDRAULIC " interface of the mass of fluid inside the tubes for tubular technologies in " SIZING " mode for two-phase heat exchanger.
Expertise:
- Added correlations from the publications of Junqi & Al. 2013 dedicated to the calculation of friction factor and partial heat exchange coefficient for "Plate-Fin Single-Phase" technology equipped with corrugated fins.